revisiting the past... the ELA M 251
- chaddavidkelly
- Jun 13, 2019
- 6 min read
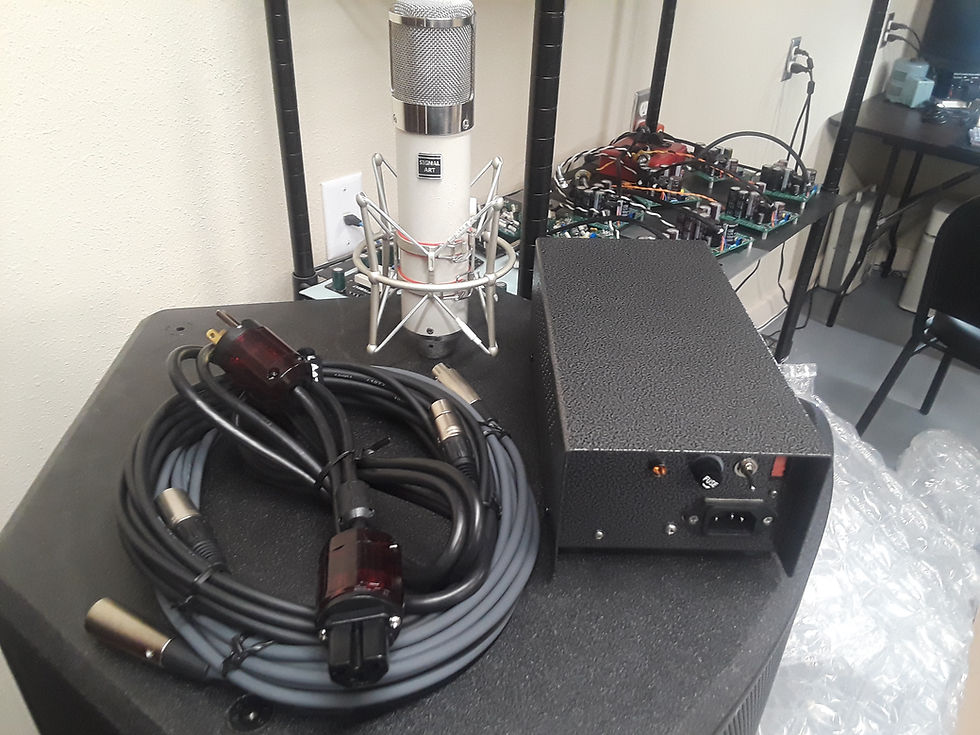
A few weeks ago I had the pleasure to hear a microphone shootout at a local studio, where for the first time I got to hear a production sample of an affordable reproduction of the classic Ela M 251 that I had helped develop for another company I used to work for. I was pleasantly pleased with how it had turned out, as I had not heard the mic since signing off on the final prototype some several years prior. It had a rich, bold sound, and may be my second favorite of those I developed or co-developed for this other company (favorite being the KM84 replica probably, which was also on display).
However, being as hopelessly OCD as I am, I still left out of there feeling like I could do it better if only I had been given more time. In any company, time is always of the essence... there are production deadlines and one is always juggling 20 things at once. But now that I work on my own schedule more or less, and could make the time, I decided to finally revisit this project and see what improvements could be made if I were able to work without restraints, so to speak.
The first thing I wanted to reverse was a compromise that is often made when dealing with mass production assembly houses in Asia. Things have to be made foolproof to assemble, to put it nicely. Over the years, I've come up with a bag of tricks to allow for this, such as strategically placed ribbon cables, transformer that are through-hole mount instead of wired (and with pin offsets so that they only have one possible orientation!). Much of this is harmless and even good; but one compromise I regret making was having most of the high-impedance section of the mic circuit integrated into the main PCB opposed to being done point-to-point manually, floated in air. The latter way is absolutely the right way to do it; however, having done it, I knew there is simply no way to have assembly places in China do this. It's just too much to ask. So I made a compromise. One that probably only resulted in a 1% sonic difference but nonetheless one that bugged me endlessly. Going back to an earlier revision of the board, and wiring this section very carefully point to point was satisfying, and I believe opens up the top end and 'air' band of the microphone by just a touch more... more open in the top end. Just ever slightly; but enough that I believe an experienced engineer would pick up on.

From there, I wanted to address self noise. Historically speaking, an Ela M 251 is about one to two dB noisier than a good U47, on a good day. It's just a given; part of that is because a 6072 valve has a much higher gain factor than a VF14m, and 'throws away' more gain from a steeper step-down transformer ratio; but that's not the only reason of course. By utilizing some very expensive and high end silver teflon wire for all of the critical wiring, and even shielding some of the audio wiring inside the PSU, I was able to get some pretty admirable results. Then by using what may be the world's quietest 6072 valve currently in production (the T.A.D. Germany 12AY7 Highgrade), this helped a lot as well. One thing I did not sign off on, and am unsure why this was done, was the use of a JJ (Czech) standard 12AY7 in the aforementioned production model. While I am a fan of JJ tubes and have spec'd their part numbers on several products before (for 3 different companies, actually), I am not sure it has the right timbre for this kind of product; and it certainly does not have a particularly low self-noise, unless the tube is seriously screened and cherry-picked. Although, to be fair, the production unit had a perfectly acceptable self noise level to me. But for me, I settled on the T.A.D. valve, which was the tube I initially had in mind years prior. I also acquired a small batch of NOS GE blackplate military spec 6072s (cleaned and tested, equivalent to the GE 5 Star brand) as well as a couple JAN GE 12AY7's which are quite similar. These will go on the more premium version of this microphone if I decide to make it a product that we sell.
No tube circuit is any better than the power supply driving it; so I did not skimp. Using a ridiculously over-sized toroid that I simply love (about 5 times the mass and 5 times the cost of whatever is used in the China-manufactured product), it ensures that the tube will always 'sing' and deliver fast, uncompressed, clean audio. Oversized, quality toroids not only have more available operating headroom but a slightly lower output impedance as well, meaning that there would be no compression of transients or any other power-related limiting factors in the mic's performance. Being toroidal, this transformer has the ability to be 'tuned' for the lowest possible noise position; but being shielded with a drain wire tied to star-ground within the PSU, it doesn't even require it!

For the capsule, I went with my own imported CEK-12 capsule that is more affordable. I have and plan to produce some models which have an American made Heiserman CK-12 that is an authentic AKG CK-12 replica, both mechanically and spot-on sonically. This model will be more expensive, obviously; but I do plan to have both a baseline edition (that is still outstanding in quality) and a premium edition that features the authentic CK-12 replica and NOS GE 6072 blackplate mil spec tube.

For the body, I went with the Beesneez Australian C12 style body. It just has such tremendous weight and heft to it; it is a bit larger, a lot heavier, and just feels so much more substantial than the decent but only so-so Asian yellow import body. It also uses their shockmount, which is quite nice.

The wood box is once again custom designed for us by our source in Germany. It's expensive; but it's lovely, and well worth it. Real wood-no laminate material!

Component voicing, as mentioned above, was done in a bit of a hurry a few years back on the production model; but this time I was able to make some refinements. I don't feel in hindsight that the Solen Fast-cap is the right choice in output capacitor. Its absolutely a fine and high-performance part; but not historically in the spirit of the original mic. As we know in audio, 'better' is not always better. I was able to pull from a personal stash of NOS PIO and metallized polypropylene capacitors that are from the era, which matched the value and characteristics a bit more nicely, I felt. These are no longer available; but I have enough on hand to do a decent sized production run.

I also used NOS polystyrenes and tantalums where appropriate, throughout; and tweaked some component values once again to balance the voicing just right. When first developing the production microphone several years back, I had a desire to extend the low end reach of the microphone. As many know, the 251 was originally marketed as a broadcast/film microphone and sort of a replacement for the U47 in Telefunken's catalog; and lacked low end because it mainly didn't need it for its intended customer. Though there is some controversy about which schematics were actually followed in production; its certainly true that a by-the-book 251 following the most commonly found published schematic will be rather anemic in the low end. I had a feeling that one could extend the low end reach of the mic without adverse effects, without taking away from the top-end magic of the 251's sound; and I still believe that to be the case. But, I slightly over-shot it by just a hair. The production version of this mic has a richer low end than this same company's '47', and that means that there is not a balance in the universe (lol). So I micro-tweaked the values of 3 different components to scale back that bottom end accentuation just a touch, in addition to having a very neutral tube; and I think the results are just perfect. It certainly does not lack bass; but the bass is no longer over-accentuated and the top end is ever slightly more open and less claustrophobic. It does not have a 'smiley face' sound, as the production model has been described by some to me.
And of course, I hand made the Gotham 7 pin, Gotham 3 pin, and IEC power cable to my own production standards.
So now, after 2+ years, I can quit losing sleep over this particular design and move on to other cool things! More to come. In the meanwhile, let me know your thoughts on the 251 and if you might be interested in getting one. I am gauging whether or not to make this an ongoing product.
obsessed as always,
Chad
Comments